
Chemical Processing
We offer a complete line of materials designed to tackle the unique challenges of maintaining process equipment and infrastructure in all areas of chemical production and processing operations. Our solutions are meant to be applied to specific problems you tackle every week to keep your part of the operation at peak performance. And our solutions are meant to be applied in your real life conditions without unrealistic expectations of the available time and resources available.
Containment
Your ability to properly contain leaks and spills of process chemicals and even possibly contaminated stormwater is critical to the continued operation of your plant. Your efforts will be focused on complete containment to protect waterways, groundwater and all other aspects of your local communities and environment.
Applications
- Sump Repairs
- Maintenance Free Joints
- Protective Coatings and Toppings
- Joint Sealing
- View All Applications
Sump Repairs
Sumps in containment areas are critical for collecting spills and preventing hazardous chemicals from escaping into the environment. However, these sumps often remain perpetually wet, making it challenging to apply and maintain protective coatings. Traditional coatings may become saturated and degrade over time, failing to protect the underlying concrete effectively. This constant exposure to harsh chemicals can lead to significant deterioration of the concrete structure.
A viable solution is the use of polymer concrete for sump repairs. Unlike conventional coatings, polymer concrete is highly resistant to chemical saturation and provides a durable, long-lasting barrier. Its application can restore the structural integrity of the sump, ensuring it functions effectively in containing spills. By opting for polymer concrete, facilities can achieve permanent repairs, reducing the frequency of maintenance and enhancing overall safety.
Related Products
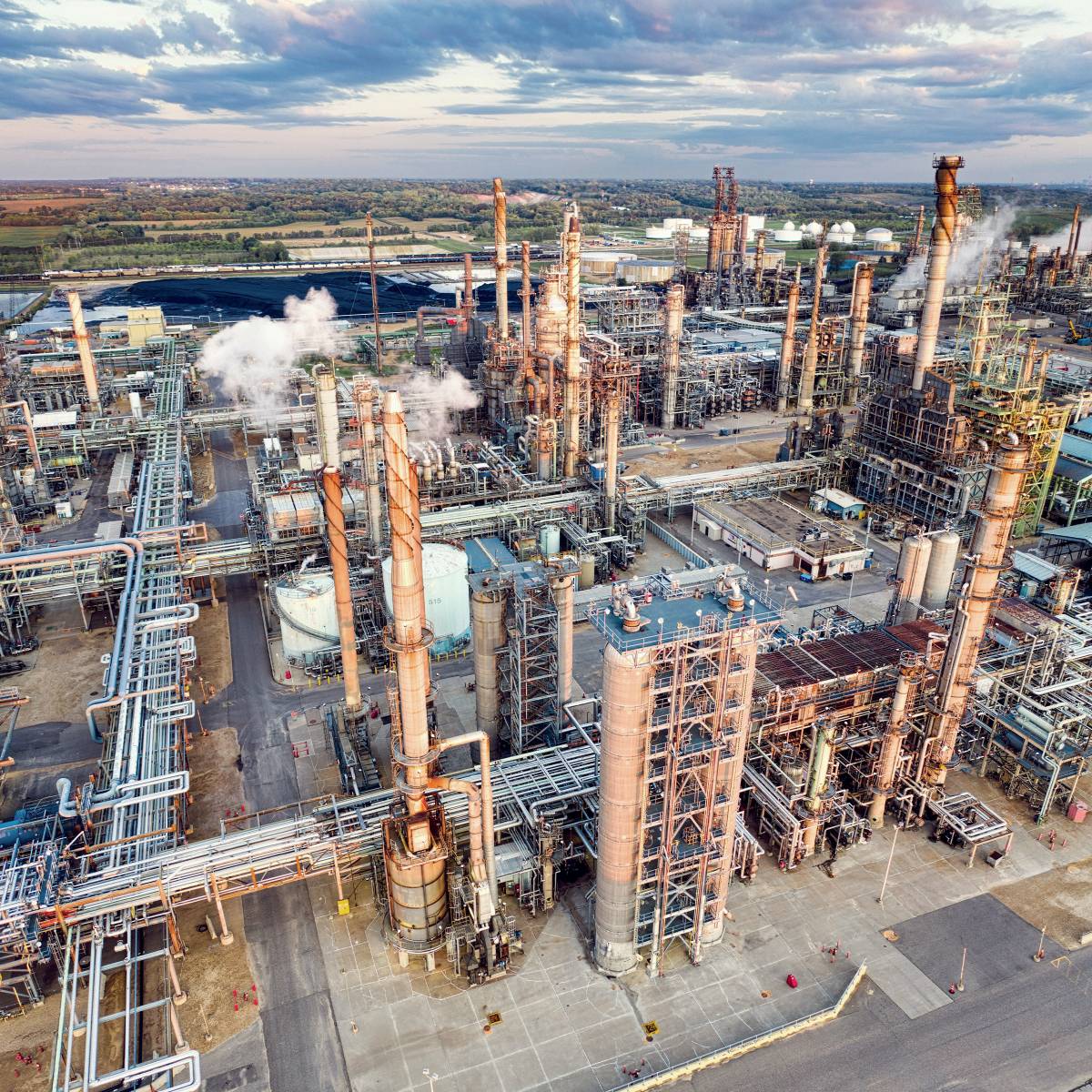
Maintenance Free Joints
When constructing new containment areas, it’s crucial to design joints that minimize maintenance requirements. Traditional joint sealants may degrade over time, necessitating regular resealing to maintain their effectiveness. This ongoing maintenance can be both time-consuming and costly.
Incorporating poured-in-place chemical-resistant seals during the construction phase can eliminate the need for frequent maintenance. These seals are designed to accommodate structural movement while maintaining a robust barrier against chemical leaks. Additionally, they can withstand heavy traffic, making them suitable for areas subjected to mechanical loads. By implementing maintenance-free joints, facilities can enhance the longevity and reliability of their containment systems, reducing downtime and maintenance costs.
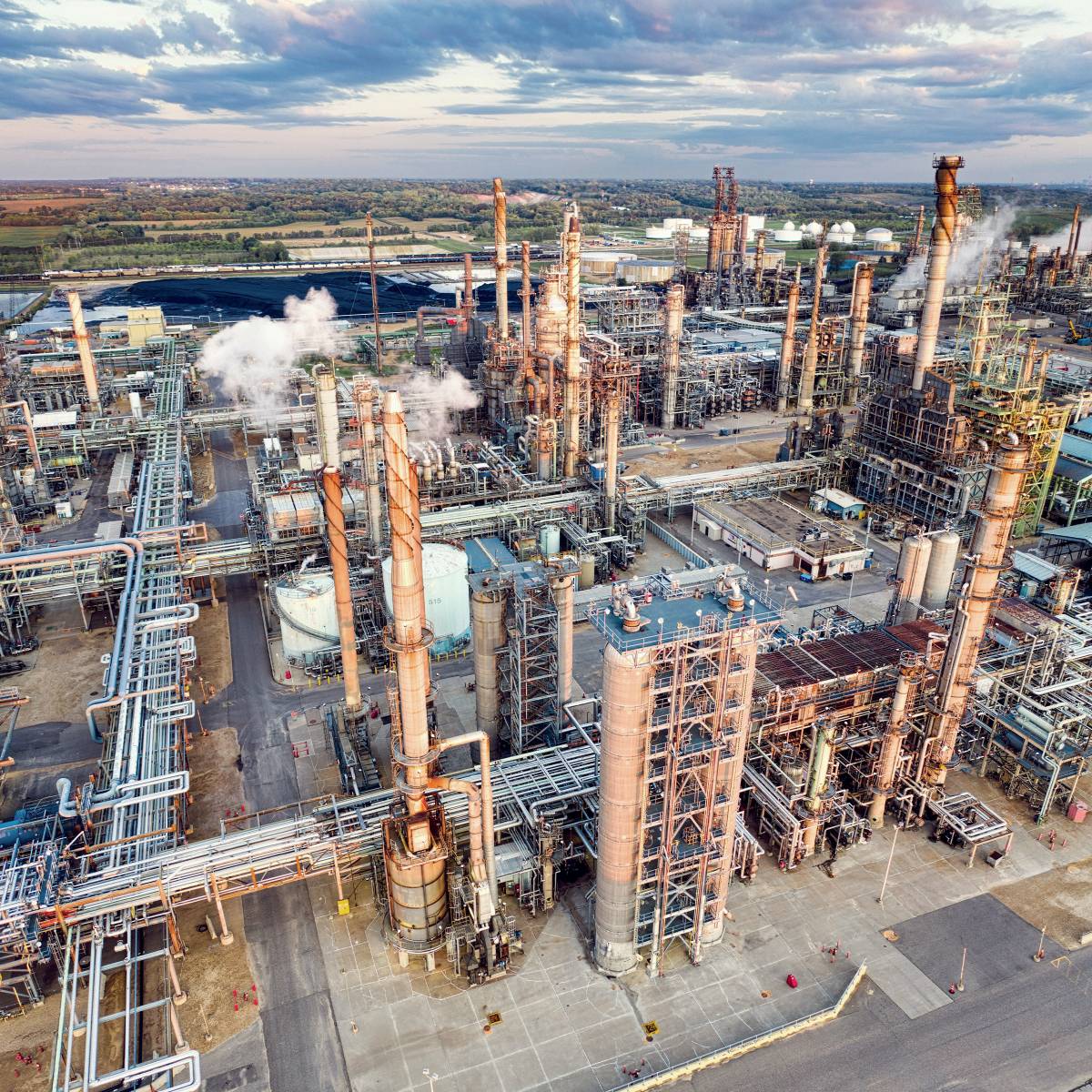
Protective Coatings and Toppings
Containment areas are subject to constant exposure to corrosive chemicals, making protective coatings and toppings essential for preserving structural integrity. Regular maintenance of these protective layers is necessary to address wear and tear, especially around high-risk areas like drains.
Utilizing a range of industrial-grade coatings, repair materials, and joint sealants can provide robust protection against chemical attacks. These products are designed to withstand the harsh conditions typical in chemical processing plants. Regular inspection and prompt repair of any damaged coatings can prevent further degradation of the underlying concrete, ensuring the containment area remains secure and compliant with environmental regulations.
Related Products
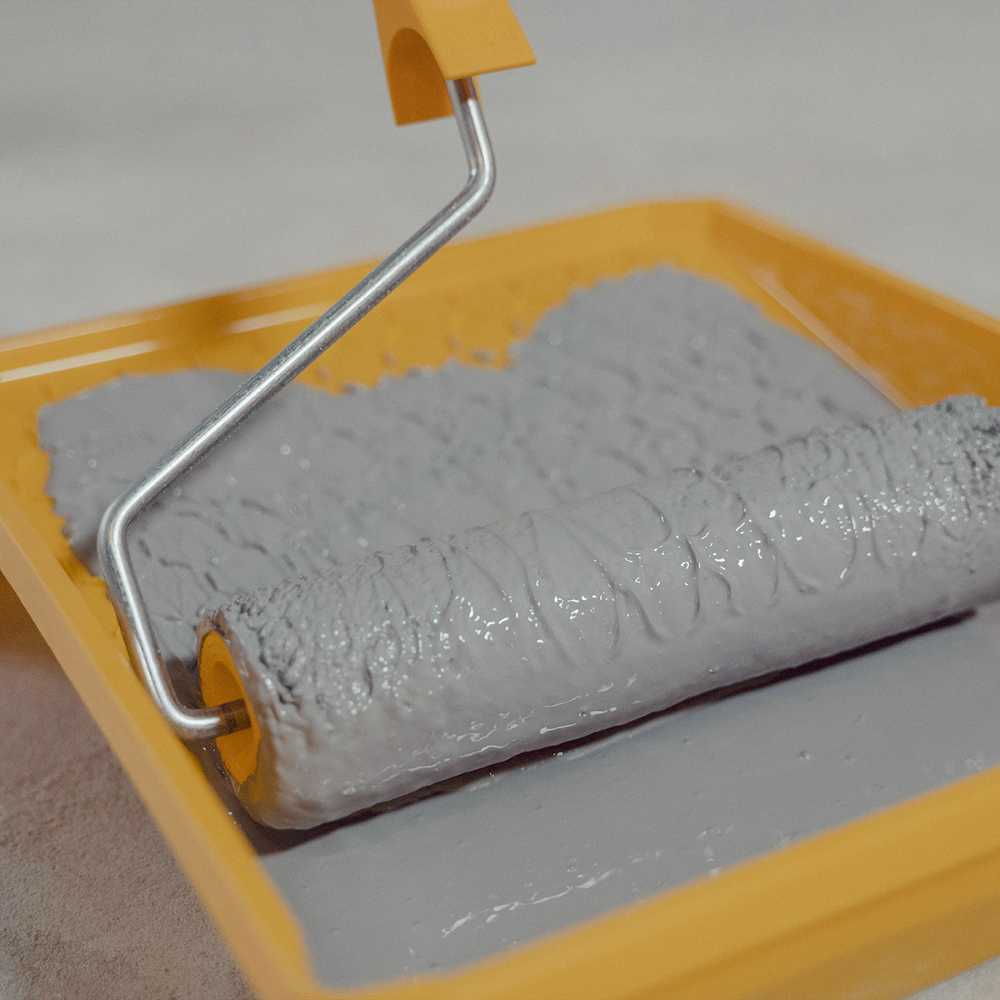
Joint Sealing
Proper joint sealing is vital to prevent leaks in concrete containment structures. Unsealed or improperly sealed joints can allow process chemicals and contaminated stormwater to escape, posing environmental hazards and compromising structural integrity.
Selecting the appropriate joint sealer requires consideration of the specific chemicals involved, exposure to environmental conditions, and the expected movement of the joint. Ensuring proper installation is equally important to maintain the effectiveness of the seal over time. By addressing joint sealing with suitable materials and techniques, facilities can significantly reduce the risk of leaks, ensuring a safer and more compliant operation.
Related Products
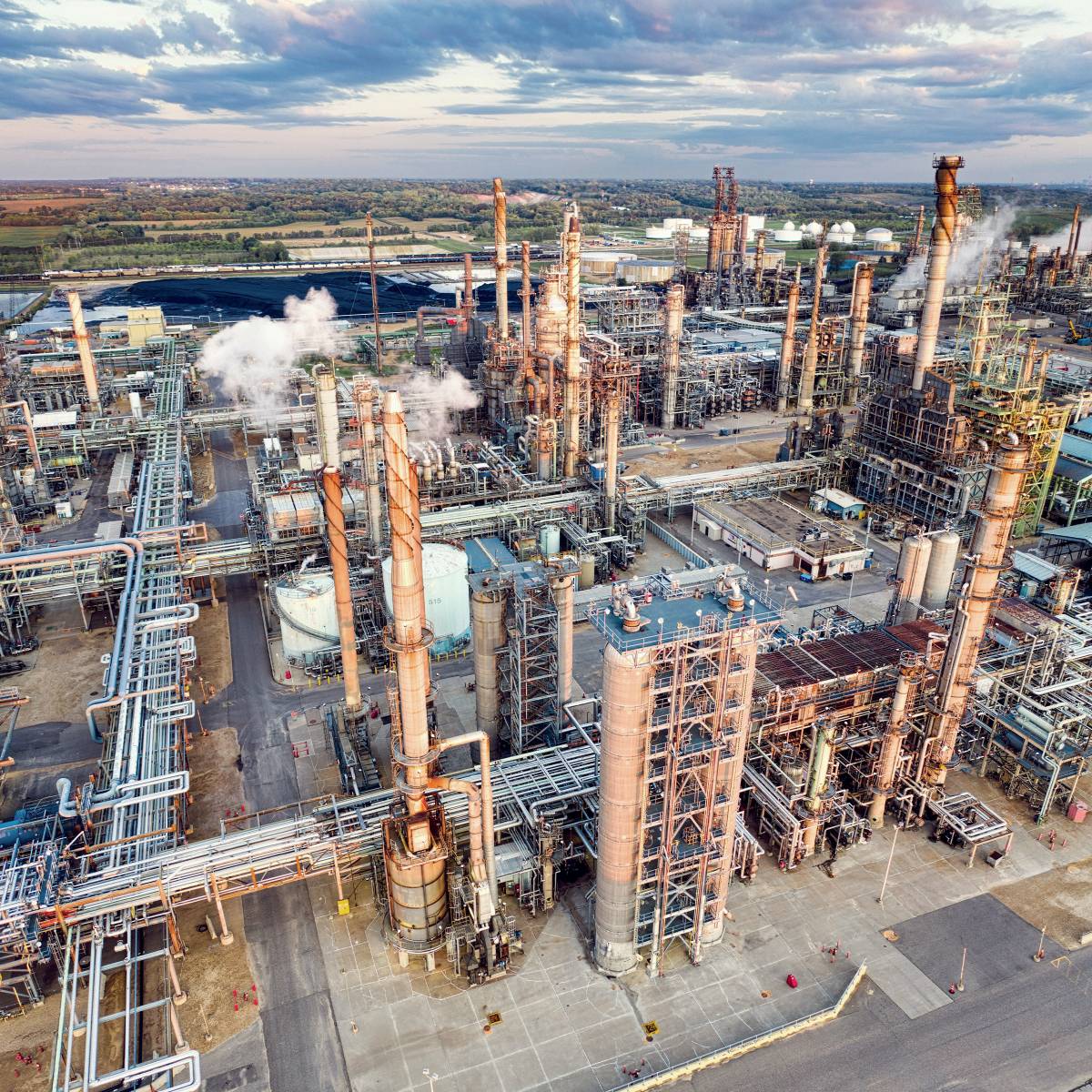
Process Areas
Maintaining the integrity of process areas in industrial facilities is crucial for operational efficiency and safety. Key aspects include process floor repairs, pump grouting, and the use of acid-proof concrete.
Applications
- Process Floor Repairs
- Pump Grouting
- Acid-proof Concrete
Process Floor Repairs
Process area floors are integral to a facility’s containment system, designed to withstand chemical exposure and facilitate safe operations. Over time, these floors may suffer from wear, chemical attacks, or mechanical damage, compromising their functionality.
Effective floor repair involves selecting appropriate materials that resist chemical penetration and provide durability. Trowelable mortars can be used to create slopes toward drains, ensuring efficient liquid runoff and preventing pooling. In low-lying areas prone to saturation, polymer concrete offers superior resistance to chemical infiltration, maintaining the floor’s integrity.
Regular inspections and timely repairs of process floors are essential to prevent minor issues from escalating into significant hazards. Implementing a proactive maintenance strategy ensures that the flooring system remains robust, supporting safe and efficient operations.
Related Products
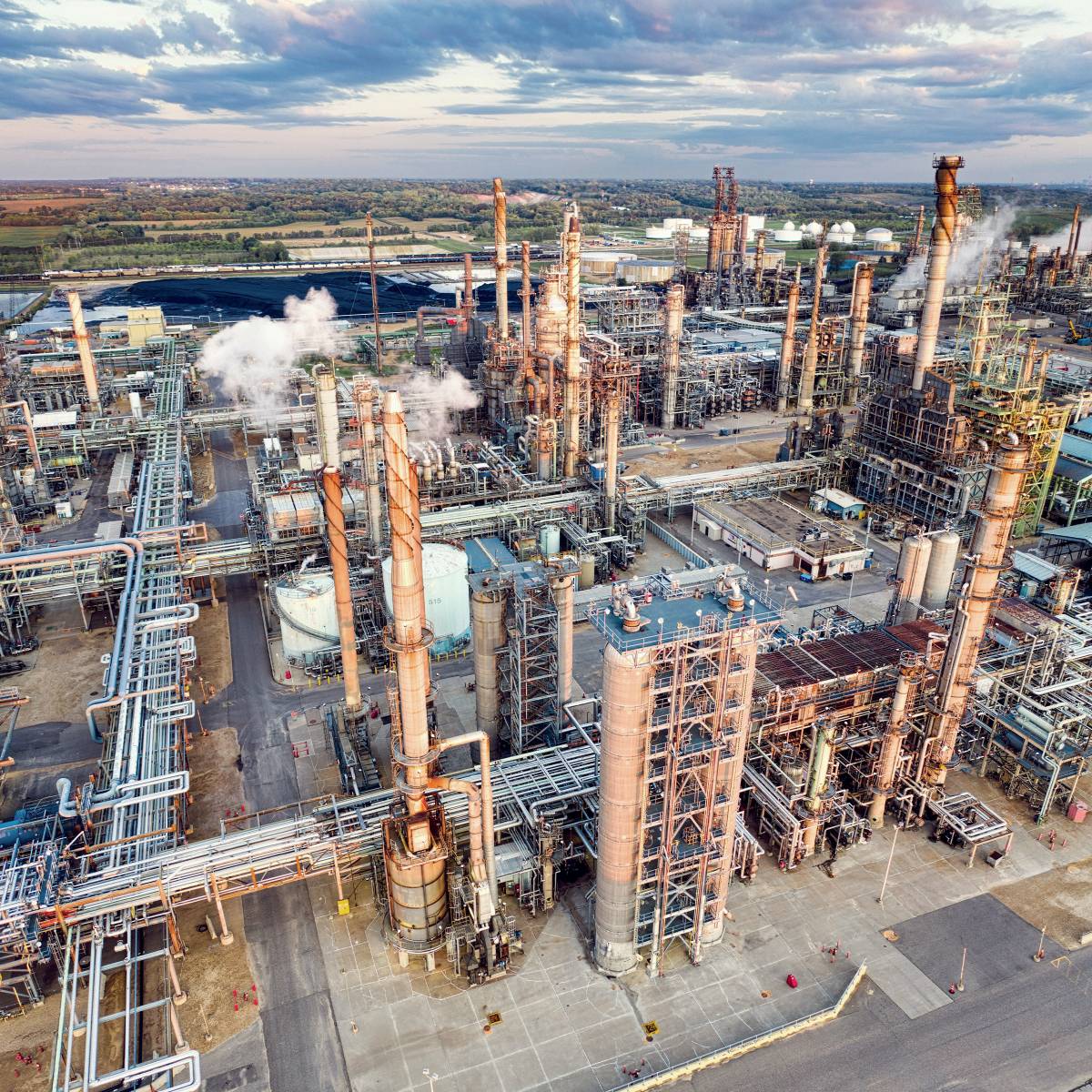
Pump Grouting
Pumps are vital components in industrial processes, and their performance heavily depends on the stability of their foundations. A compromised foundation can lead to misalignment, vibrations, and ultimately, equipment failure.
Pump grouting involves securing the pump to its foundation using materials that can withstand operational stresses and potential chemical exposure. Selecting a grout that is resistant to the specific chemicals handled by the pump is crucial, as leaks or spills can deteriorate standard grouting materials.
Proper pump grouting enhances equipment stability, reduces maintenance costs, and extends the lifespan of the pump. By planning for potential chemical exposure and choosing appropriate grouting materials, facilities can safeguard against operational disruptions and ensure the longevity of their equipment.
Related Products
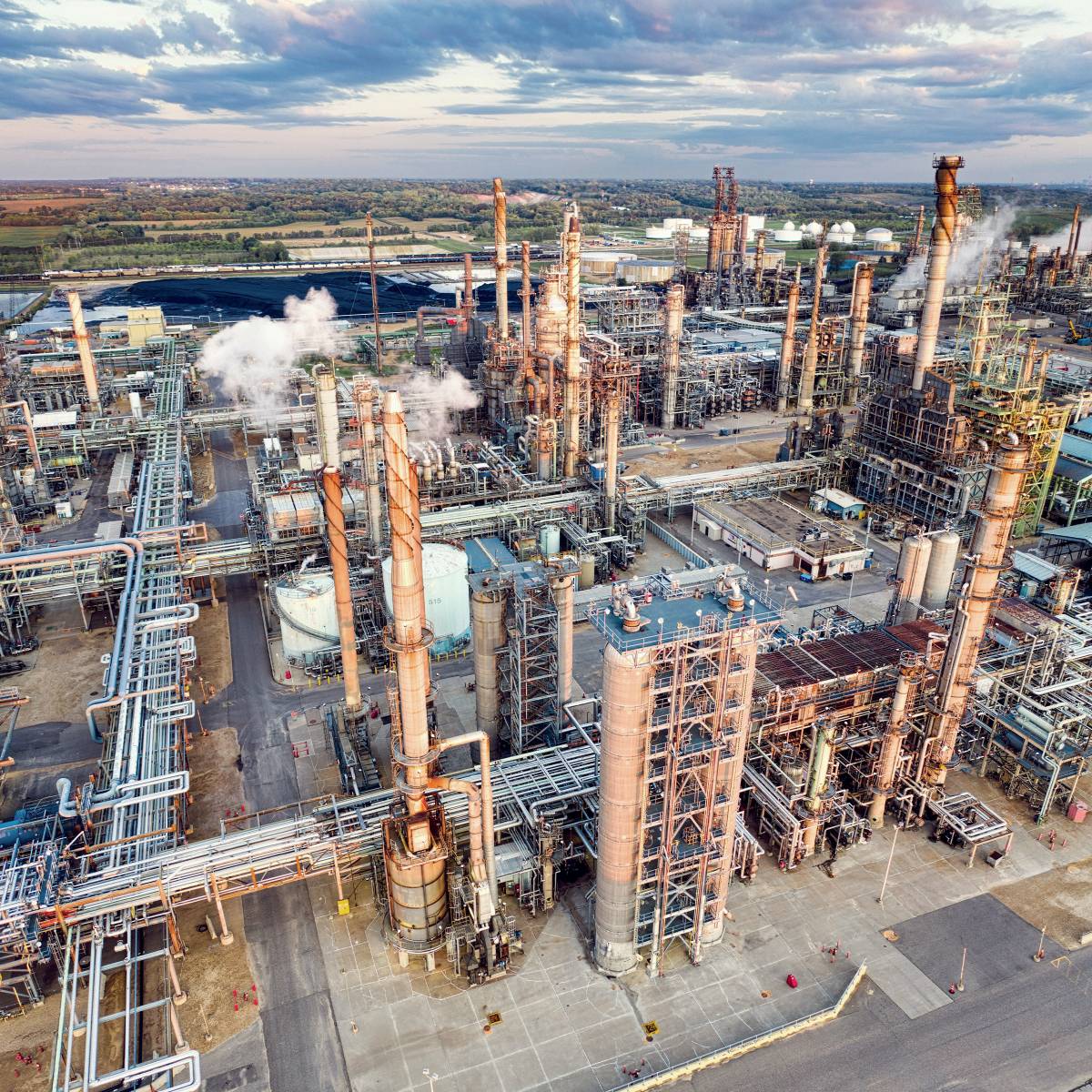
Acid-proof Concrete
Concrete is a fundamental material in industrial infrastructure, used in pump pads, support piers, trenches, and more. However, standard concrete is susceptible to degradation when exposed to harsh chemicals commonly found in industrial settings.
Acid-proof concrete is engineered to resist chemical attacks without the need for additional coatings. Its enhanced durability makes it suitable for environments where chemical exposure is frequent and severe. Utilizing acid-proofing in construction and repairs ensures that structures maintain their integrity and require less maintenance over time.
Incorporating acid-proof concrete into facility design and maintenance strategies provides a robust solution for areas prone to chemical exposure, enhancing safety and structural longevity.
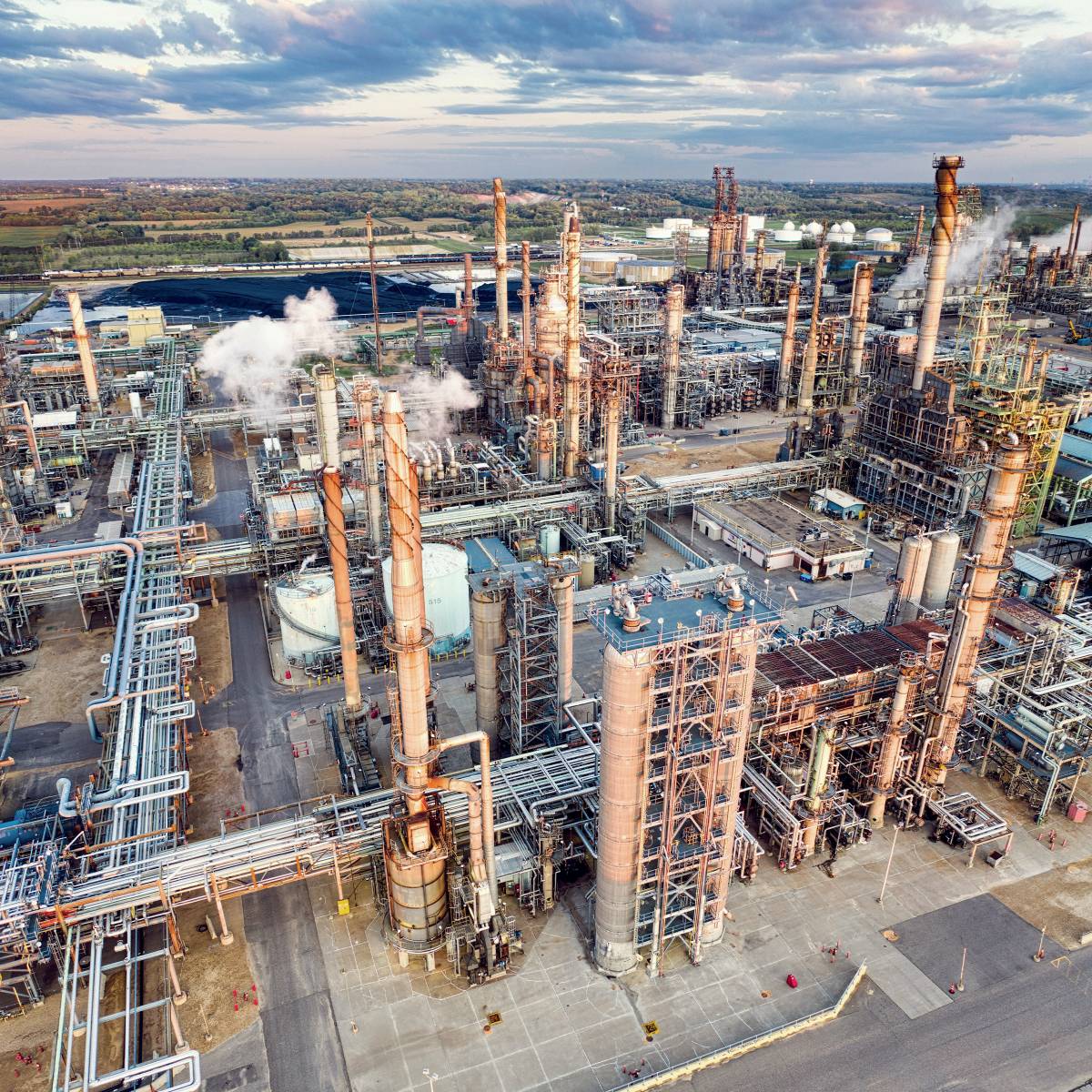
Storage
Applications
- Cracked Weld Repair
- Tank Chime Repair
- Preventing Coating Damage
- Warehouse Floor Coatings
- View All Applications
Cracked Weld Repair
Cracked welds in storage tanks are more than just a minor inconvenience — they can pose significant operational and safety risks. As the primary containment for your processes, these tanks must maintain their structural integrity at all times. While traditional welding methods are often used to repair cracks, they may not always provide a long-lasting solution, particularly in older or heavily used tanks. By applying a reinforced metal-filled epoxy paste, you can achieve an effective seal that restores the tank’s structural integrity and prevents leaks. This method is not only efficient but also minimizes downtime, reduces the frequency of costly repairs, and extends the overall lifespan of the tanks. Addressing weld cracks promptly is essential to maintaining safe and efficient operations.
Related Products
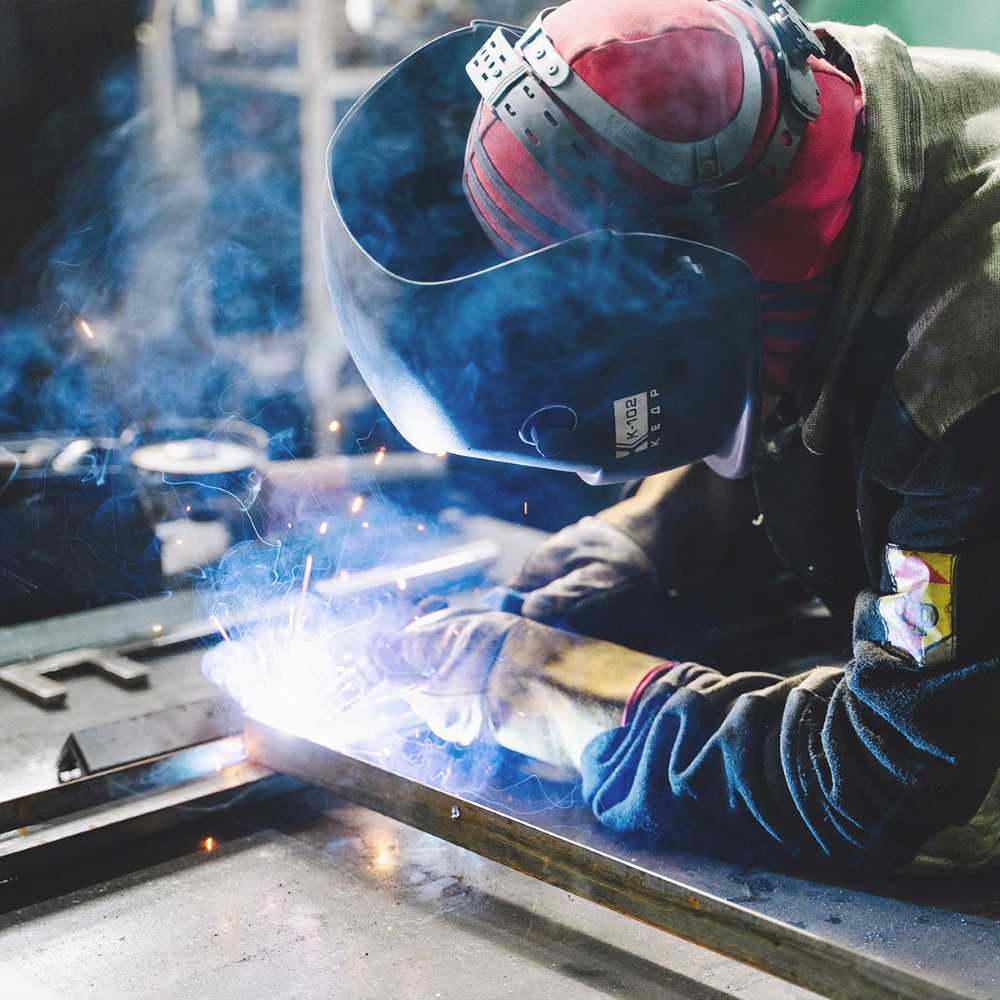
Tank Chime Repair
The tank chime, where the storage tank walls meet the base, is a critical structural component that requires careful maintenance. This area bears significant stress, particularly in tanks holding liquid, and any damage or weakening can lead to leaks or structural failures. Routine inspections are vital to identify early signs of wear or damage. Addressing these issues proactively prevents small problems from escalating into costly repairs or operational downtime. Strengthening the chime area not only ensures the structural stability of the tank but also increases its lifespan. By prioritizing chime repairs, you can maintain the safety and functionality of your storage systems while reducing long-term maintenance costs.
Related Products
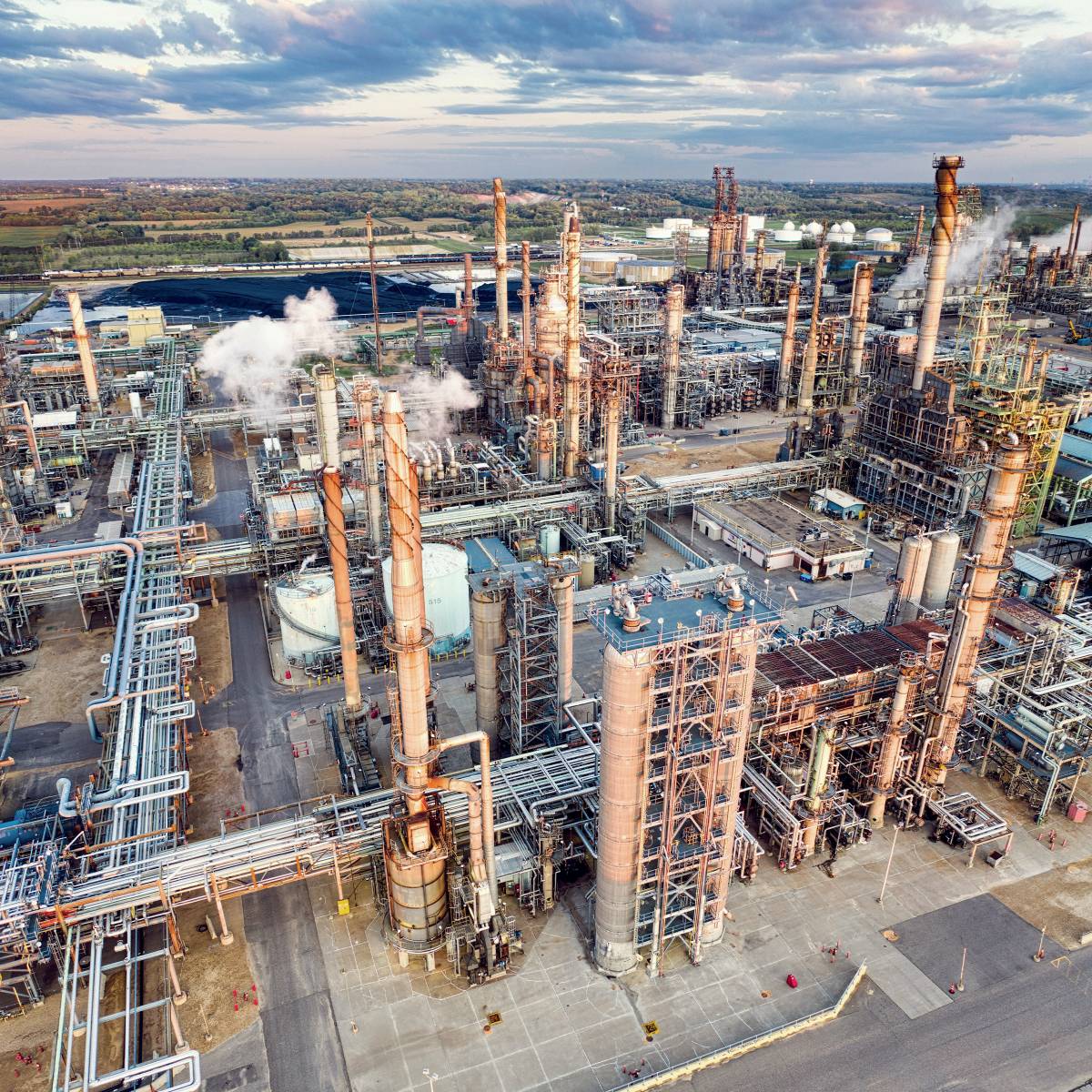
Preventing Coating Damage
Sloped areas in storage facilities are essential for effective spill management, but they can also create unique challenges. Uneven surfaces and slopes near trenches, drains, and other spill management features can cause pallets, forklifts, and other equipment to scrape or damage thin-film coatings. Over time, this wear can compromise the protective layer of your floors, leaving the substrate exposed to damage. To address this, filled coating systems such as silica or aluminum oxide applications can be used to enhance the durability of these surfaces. These coatings provide increased resistance to wear and tear, making them ideal for high-traffic areas. By investing in robust floor coatings, you protect your floors, reduce maintenance costs, and create a safer, more efficient work environment.
Related Products
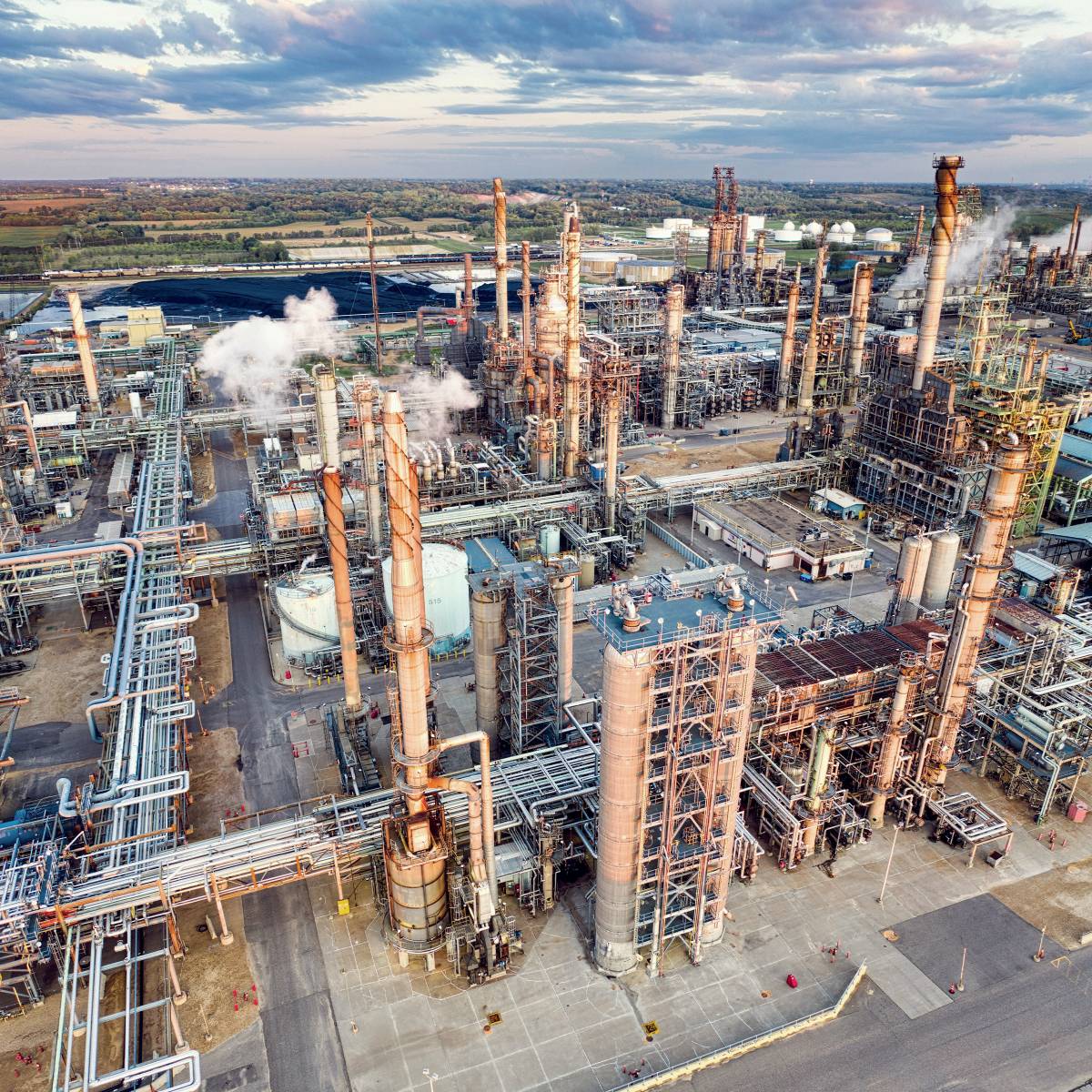
Warehouse Floor Coatings
The condition of your warehouse floors is integral to the smooth operation of your facility. Damaged floor areas, particularly around joints, transitions, and high-traffic zones, can lead to serious safety risks, operational disruptions, and potential product damage. Common trouble spots like doorways, ramps, and loading areas are especially prone to impacts and wear. Installing durable floor coatings and implementing regular maintenance can significantly enhance the resilience and lifespan of these critical areas. Not only do high-quality coatings ensure a smooth and even surface for equipment, but they also minimize the risk of accidents and spills. Proactively maintaining your warehouse floors reduces downtime, protects your products, and ensures a safe working environment for your team.
Related Products
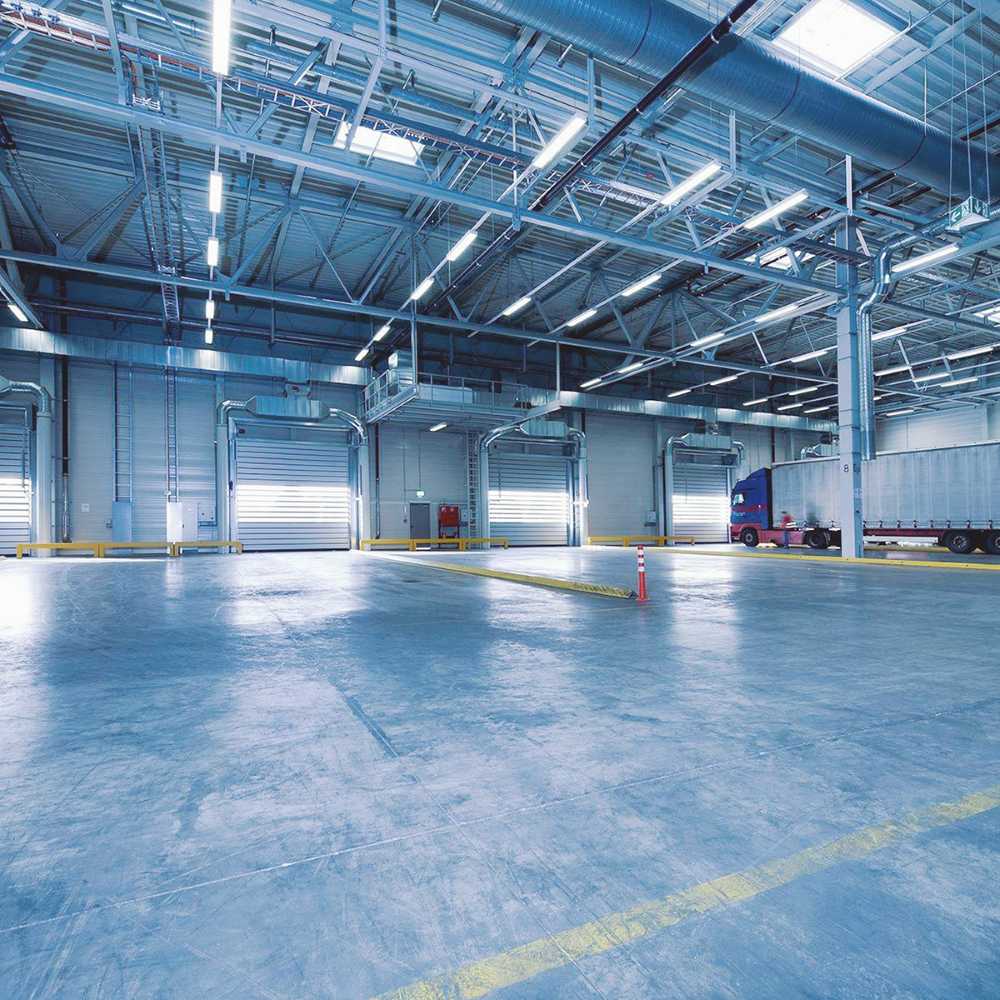
Transfer
The efficiency and safety of material transfer areas within industrial facilities is paramount. These zones, where raw materials arrive and finished products depart, must be meticulously maintained to uphold operational integrity and protect personnel. Key considerations include the application of appropriate joint sealants to withstand heavy vehicular traffic and the implementation of non-slip coatings in loading and unloading zones to prevent accidents.
Applications
- Joint Sealants for Truck Traffic
- Non-slip Coatings for Tanker Loading and Unloading Areas
Joint Sealants for Truck Traffic
In industrial settings, the durability of floor joints is critical, especially in areas subjected to constant heavy truck and forklift movement. Over time, this traffic can deteriorate joint integrity, leading to potential containment breaches and costly repairs. Selecting the appropriate sealant or filler tailored to the specific type of traffic and chemical exposure is essential. Advanced materials are available that offer exceptional resilience against heavy loads and chemical interactions, ensuring long-term performance and reducing maintenance frequency.
Related Products
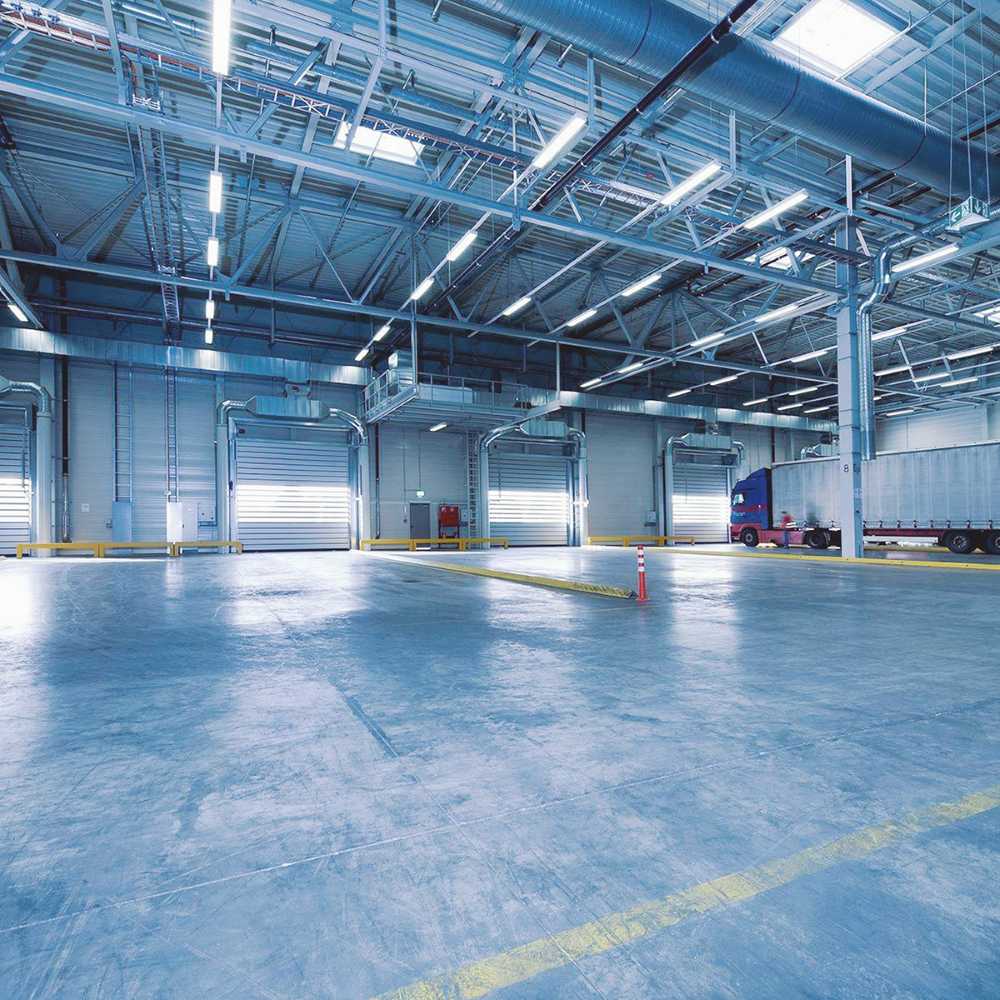
Non-slip Coatings for Tanker Loading and Unloading Areas
Loading and unloading zones are high-risk areas where spills from transfer hoses or leaking seals are inevitable. These spills can create slippery surfaces, posing significant safety hazards to personnel. Implementing non-slip coatings in these areas is a proactive measure to mitigate such risks. Modern non-slip coatings are engineered to provide superior traction, even in the presence of liquids, thereby preventing accidents and ensuring compliance with safety regulations. Regular assessment and maintenance of these coatings are vital to sustain their effectiveness over time.
Related Products
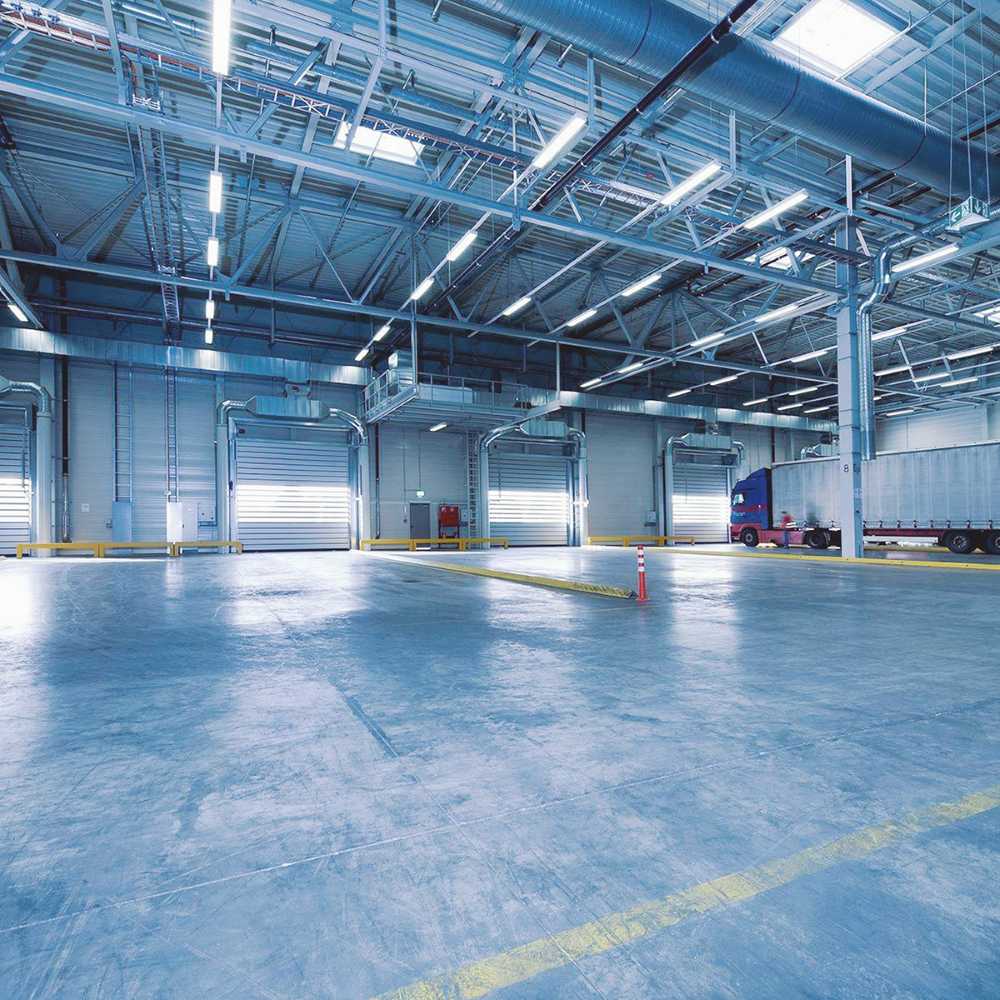